What is Fluid Structure Interaction (FSI)?
- Omkar Bajpai
- Feb 14
- 4 min read
Ever Wondered Why Bridges Sway or Aircraft Wings Flex?
Think of wind blowing over a bridge making it oscillate in a very subtle way. An aeroplane wing moves in turbulent skies like it is bending without much force. A stent inserted inside an artery expands and contracts according to blood. All these have something in common, which is called Fluid-Structure Interaction (FSI).
FSI is a fundamental phenomenon where fluids (air, water, blood) and solid structures (bridges, aircraft, arteries) interact dynamically, and in that dynamic interaction, they influence the behaviour of each other.
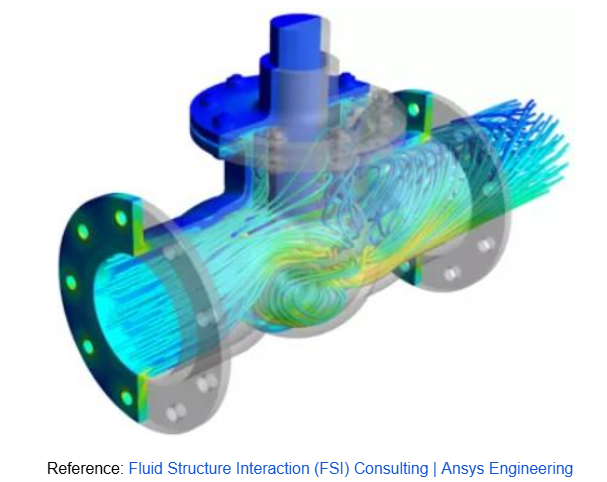
It thus becomes clear that this intricate dance between the forces applied by the fluid and the response by the structure combines into several real-world applications within the aerospace, civil engineering, automotive, and MedTech industries.
Why Does FSI Matter?
The truth of structures in a world that drives their all-purpose efficiency, safety, and durability has substance only when they are understood vis-a-vis their response under fluid forces. This leads to the utilisation of the FSI simulation by engineers and researchers to come up with a smarter and more resilient design elements under which everything works, say an aircraft stability and biomedical devices performing as required in the real world.
Advances in high-performance computing, simulation based on artificial intelligence, and CFD have transformed the FSI paradigm for industries striving to innovate and precision engineer.

The Science Behind FSI
Fundamentally, the FSI means a two-way interaction between a solid and a fluid coexisting in the same environment. The fluid applies pressures and shear forces on the structure, causing it to deform, and the deformation in turn generates flow changes associated with the fluid. Thus, continuous feedback between the structure and fluid is established.
Key Concepts involved:
Bidirectional Coupling: fluid forces affect structures; structural deformations in turn affect fluid movement.
Transient Interactions: most fluids-solid interaction problems are associated with some time evolution and thus require dynamic analysis.
Multi-Physics Approach: FSI involves the principles of fluid dynamics, the mechanics of structures, and thermal effects.
All these together make FSI a very complicated but important area of engineering, with an energy, momentum, and force exchange between material and an environment.
Day to Day life Examples:
Aircraft Wing Flutter Analysis: Did you ever observe the mid-air flex of aeroplane wings? That's the beauty of FSI, as it helps engineers design wings that fulfil their role in adding aerodynamic loads with efficiency.
Car Crash Simulations: The car manufacturers perform impact analyses with fluids air, coolant and fuel affected by the vehicle structures so that they can improve prototypes of passenger safety.
EV Battery Cooling: With the advent of electric vehicles, FSI has also entered the arena of thermal management and optimization of battery cooling systems for the duration and efficiency of an electric vehicle.
MedTech Industry:
Blood Vessel Reflow and Stenting: An FSI simulation is used by surgeons to ensure the adaptation of stents for blood flow to minimize their risk of failure.
Artificial Heart Valves: Using FSI-assisted models, engineers design valves imitating natural blood flow with higher acceptance to implant procedures.
Airway-Lung Interaction: With the help of FSI simulations, new and improved ventilators give nearly accurate airflow to patients while undergoing treatment for better efficiency.

Civil and Structural Engineering:
Bridge Stability: The famous Tacoma Narrows Bridge failure in 1940, brought about by oscillations stirred up by wind, highlighted the importance of FSI in bridge design.
Hydropower Plants: FSI Studies are committed to elucidating how currents in water can affect turbine blades in hydropower production.
Tall Buildings: Greater stability of tall buildings against the forces of high winds and seismic activity is warranted by employing design theory of FSI.
Case Study: India’s Chenab Bridge Wind Load Simulation
The Chenab Bridge in India is an epitome of the engineering marvels created by FSI. With the help of FSI simulations, engineers could study the effect of severe winds from the great Himalayas on the bridge and use those results to modify its aerodynamic stability so that it could resist extreme wind pressures and other ecological conditions.
MedTech: FSI in Artificial Heart Valves
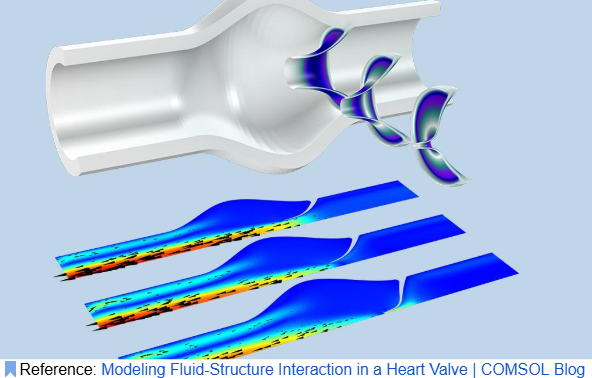
A premier company engaged in the manufacture of medical devices has successfully applied FSI simulations for the refinement of artificial heart valve designs, such that efficient blood flow was obtained while minimizing the chances of clot formation.
Engineers tested various geometries under typical dynamic conditions of blood flow and significantly improved the durability of the valve and patient safety. This is a transformation in implant systems for next-generation cardiovascular devices.
How Do Engineers Simulate FSI?
Engineers can now use the latest technologies to predict and optimize the behavior of
fluid-structure interaction (FSI) using computational modelling techniques. The industry-favorite modeling tools are Siemens Simcenter, Ansys Fluent, and OpenFOAM. They provide reliable real-time simulations of FSI situations.
They are of two types:
Weak Coupling: Applicable for small deformations, the solid and fluid solving separately.
Strong Coupling: Required when there are significant deformations and solve both domains simultaneous for results.
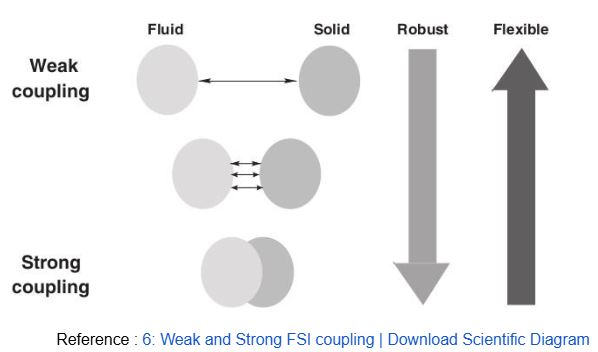
Challenges in FSI Simulation:
Computational Power: FSI models need large computing resources for simulating real-life conditions.
Mesh Deformation Problems: When structures deform their shapes, the computational mesh also has to be deformed which adds to the complexity.
Solver Stability: Numerical Solvers should remain accurate during the most complex interactions between fluid and solid.
As the bar of technology pushes itself farther and farther into the future, it is now quite clear that FSI is no longer just an idea, but rather the invisible force that makes all innovation possible.
Further Reading and Reference:
Bathe, K.J. Finite Element Procedures – Comprehensive insights into structural mechanics.
ANSYS Fluent and Abaqus Documentation – Guides on FSI simulations.
Case Study: FSI in Stent Design – Journal of Medical Engineering, 2023.
Market Growth in FSI Simulations – 2024 Industry Report.
FSI in Aerospace Wing Design – Aerospace Journal, 2022.
Chenab Bridge Wind Load Study – Indian Infrastructure Journal, 2023.
Comments